Troubleshooting Industrial Pumps: Top 15 Common Problems and Solutions
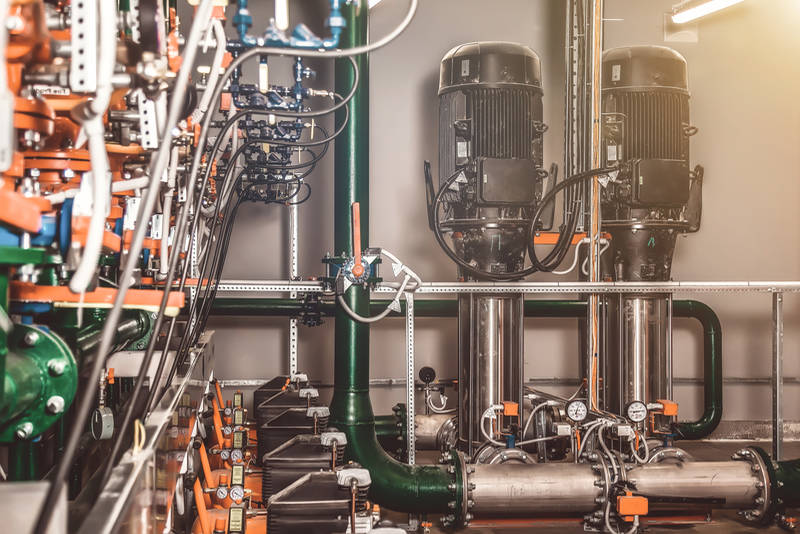
Industrial pumps play a crucial role in various sectors, from manufacturing to agriculture, by facilitating the movement of fluids. However, like any machinery, they encounter issues that can disrupt operations and lead to downtime and costly repairs. In this comprehensive guide, we’ll delve into the top 15 common problems faced by various types of industrial pumps, ranging from centrifugal to submersible pumps, and provide actionable solutions backed by stats and step-by-step procedures.
1. Cavitation:
- Problem: Cavitation occurs when the pump’s suction pressure drops below the vapor pressure of the fluid, leading to the formation and collapse of vapor bubbles, causing erosion and noise.
- Solution: Increase suction pressure by adjusting impeller size or operating speed, ensure proper NPSHa (Net Positive Suction Head available), or install a vacuum breaker to prevent vapor formation.
2. Pump Leakage:
- Problem: Leakage at pump seals, gaskets, or connections can result in fluid loss, environmental hazards, and reduced pump efficiency.
- Solution: Inspect and replace damaged seals or gaskets, tighten connections, and consider upgrading to mechanical seals for improved reliability.
3. Impeller Damage:
- Problem: Wear or damage to impeller blades can lead to decreased pump performance, increased vibration, and premature failure.
- Solution: Regularly inspect impeller condition, replace worn or damaged blades, and ensure proper alignment to minimize stress and vibration.
4. Air Binding:
- Problem: Air trapped within the pump casing or suction line prevents efficient fluid movement, leading to reduced flow and cavitation risk.
- Solution: Vent air from the system, ensure proper priming, and install air release valves or bleeders to prevent air accumulation.
5. Overheating:
- Problem: Excessive heat buildup in the pump can damage seals, bearings, and motor components, resulting in downtime and costly repairs.
- Solution: Improve cooling system efficiency, reduce pump speed, monitor motor temperature, and ensure proper lubrication to prevent overheating.
6. Vibration:
- Problem: Excessive vibration indicates misalignment, worn bearings, or cavitation, leading to reduced pump lifespan and increased maintenance costs.
- Solution: Perform vibration analysis to identify root causes, realign pump and motor shafts, replace worn bearings, and address cavitation issues.
7. Corrosion:
- Problem: Corrosive fluids can deteriorate pump materials, leading to leaks, reduced performance, and contamination risks.
- Solution: Select corrosion-resistant materials, apply protective coatings, and implement preventive maintenance measures such as flushing and chemical treatments.
8. Seal Failure:
- Problem: Seal failure can result in fluid leakage, contamination, and environmental hazards, posing safety risks and requiring costly repairs.
- Solution: Monitor seal condition regularly, replace worn or damaged seals promptly, and consider upgrading to dual or tandem seals for enhanced reliability.
9. Bearing Failure:
- Problem: Bearing failure due to overload, misalignment, or lack of lubrication can lead to pump downtime, increased energy consumption, and costly repairs.
- Solution: Implement a proactive lubrication schedule, monitor bearing temperature and vibration, and address root causes such as misalignment or overloading.
10. Erosion and Abrasion:
- Problem: Erosion and abrasion caused by abrasive fluids or solids in suspension can degrade pump components, leading to reduced efficiency and shortened lifespan.
- Solution: Select wear-resistant materials for pump components, install abrasion-resistant coatings, and implement filtration or sedimentation systems to remove solids from the fluid.
11. Low Flow or No Flow:
- Problem: Low flow or no flow conditions can result from blockages, air pockets, or insufficient NPSHa, leading to pump damage and operational issues.
- Solution: Check for blockages in suction and discharge lines, vent air from the system, and ensure adequate NPSHa by adjusting system parameters or upgrading pump size.
12. Motor Overload:
- Problem: Excessive load on the pump motor can lead to overheating, insulation failure, and motor burnout, causing downtime and costly replacements.
- Solution: Monitor motor current and temperature, reduce pump speed or impeller size to match system requirements, and ensure proper motor alignment and lubrication.
13. Seal Contamination:
- Problem: Contamination of pump seals by debris, abrasive particles, or incompatible fluids can compromise seal integrity, leading to leaks and seal failure.
- Solution: Implement proper filtration and straining systems, flush the system regularly to remove contaminants, and use compatible fluids to minimize seal degradation.
14. Suction Pipe Design:
- Problem: Inadequate suction pipe design can result in air entrainment, cavitation, and reduced pump performance, affecting overall system efficiency.
- Solution: Optimize suction pipe diameter and length, minimize bends and restrictions, and ensure proper pipe alignment and support to maintain steady flow and prevent air ingress.
15. Electrical Issues:
- Problem: Electrical faults such as short circuits, motor insulation failure, or power supply fluctuations can disrupt pump operation and pose safety risks.
- Solution: Perform regular electrical inspections and maintenance, install surge protection devices, and ensure proper grounding and wiring connections to minimize electrical issues.
Industrial pumps are essential components in various applications, but they are prone to various problems that can impact performance and reliability. By understanding the common issues and implementing proactive maintenance and troubleshooting strategies, operators can minimize downtime, reduce maintenance costs, and optimize pump efficiency. Regular inspection, monitoring, and timely intervention are key to ensuring smooth pump operation and maximizing equipment lifespan in industrial settings.
You can also reach out to us with any questions you have or ask for a quote.