Maximizing Pump Efficiency: A Comprehensive Guide to Improving Industrial Pump Performance
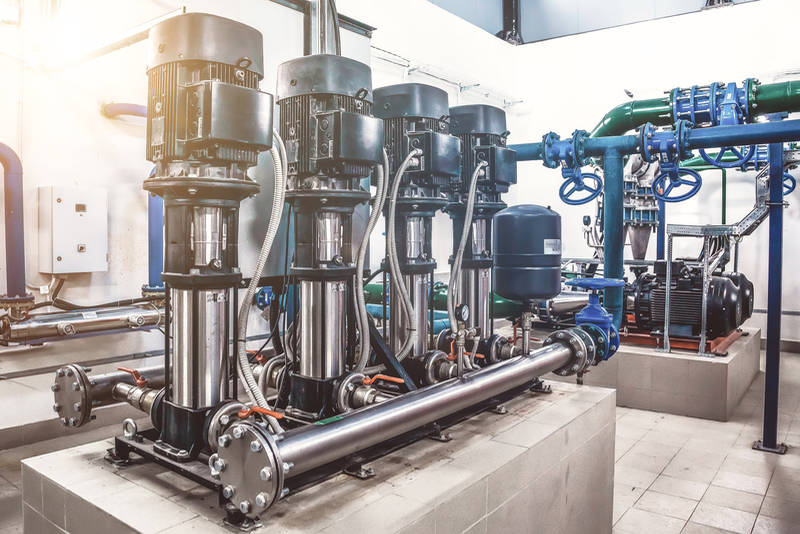
Industrial pumps are the workhorses of many sectors, from manufacturing and agriculture to mining and municipal water treatment. However, inefficient pump operation can lead to significant energy wastage, increased operational costs, and premature equipment failure. In this comprehensive guide, we’ll explore proven strategies and techniques to enhance industrial pump efficiency, leading to cost savings, extended equipment lifespan, and improved overall performance.
Conduct a Pump System Assessment:
- Begin by conducting a thorough assessment of your pump system, including pump selection, installation, and operating conditions.
- Analyze system parameters such as flow rate, pressure, fluid properties, and operating hours to identify inefficiencies and optimization opportunities.
- Utilize tools like pump system assessment software or consult with experts to gain insights into potential improvements.
Optimize Pump Selection and Sizing:
- Selecting the right pump for the application is crucial for efficiency. Choose pumps with optimal efficiency curves that match system requirements.
- Avoid oversized pumps, as they can lead to higher energy consumption and operating costs. Utilize pump affinity laws to adjust pump speed or impeller size for optimal performance.
- Consider variable frequency drives (VFDs) for pumps to adjust speed according to demand, reducing energy consumption during low-demand periods.
Improve Pump Maintenance Practices:
- Implement a proactive maintenance schedule to ensure pumps operate at peak efficiency. Regularly inspect and lubricate bearings, check seals and gaskets for leaks, and monitor motor performance.
- Conduct vibration analysis and thermal imaging to detect potential issues early and prevent costly breakdowns.
- Train maintenance personnel on proper pump maintenance procedures to ensure consistency and effectiveness.
Enhance Hydraulic Efficiency:
- Optimize pump hydraulics by reducing friction losses and improving fluid dynamics within the system.
- Smooth out piping bends and transitions, minimize restrictions, and ensure proper pipe sizing to reduce pressure drop and energy loss.
- Install efficient pipe fittings, such as elbows and valves, and consider upgrading to low-friction materials like composite or ceramic for piping components.
Implement Energy-Efficient Technologies:
- Explore energy-efficient technologies and innovations to enhance pump performance and reduce energy consumption.
- Consider upgrading to high-efficiency motors, such as premium efficiency or ultra-efficient motors, to achieve significant energy savings over time.
- Install energy recovery systems, such as regenerative drives or pressure exchangers, to capture and reuse energy that would otherwise be wasted during pump operation.
Monitor and Analyze Pump Performance:
- Utilize pump performance monitoring tools and systems to track key performance indicators (KPIs) such as flow rate, pressure, power consumption, and efficiency.
- Implement real-time monitoring and remote diagnostics capabilities to detect performance deviations and potential issues early, enabling timely intervention.
- Analyze pump performance data over time to identify trends, patterns, and areas for improvement, and adjust operating parameters accordingly.
Invest in Training and Education:
- Provide training and education for pump operators and maintenance personnel to improve their understanding of pump operation, maintenance, and optimization techniques.
- Foster a culture of continuous improvement and knowledge sharing within the organization to empower employees to identify and implement efficiency-enhancing initiatives.
- Stay abreast of industry developments, best practices, and emerging technologies through training programs, seminars, and professional networking opportunities.
Track and Measure Cost Savings:
- Quantify the cost savings achieved through efficiency improvements by tracking energy consumption, maintenance costs, downtime reduction, and equipment lifespan extension.
- Calculate return on investment (ROI) for efficiency enhancement initiatives to justify investments and prioritize future optimization efforts.
- Benchmark pump performance against industry standards and best practices to gauge performance relative to peers and identify further improvement opportunities.
Improving industrial pump efficiency is not only essential for reducing operational costs and enhancing competitiveness but also for minimizing environmental impact and maximizing resource utilization. By adopting a systematic approach to pump system optimization, including pump selection, maintenance practices, technology adoption, and performance monitoring, organizations can achieve significant cost savings, increase equipment lifespan, and enhance overall operational efficiency. Investing in efficiency-enhancing initiatives not only yields immediate benefits but also ensures long-term sustainability and resilience in today’s dynamic industrial landscape.
You can also reach out to us with any questions you have or ask for a quote.