Top 10 Questions You Should Ask When Considering An Industrial Pump
Industrial pumps are critical components in most industries, from HVAC to manufacturing and agriculture to water treatment and oil refining. Selecting the right pump for your industrial application will impact efficiency, productivity, and overall costs. However, the market is flooded with options and choosing the most suitable manufacturer and technology can be challenging. To aid in this decision-making process, here are the top 10 questions you should ask when considering an industrial pump, along with detailed answers to each:
1. What is the Nature of the Fluid to be Pumped?
Understanding the properties of the fluid is the first step to selecting an appropriate pump. Consider factors such as:
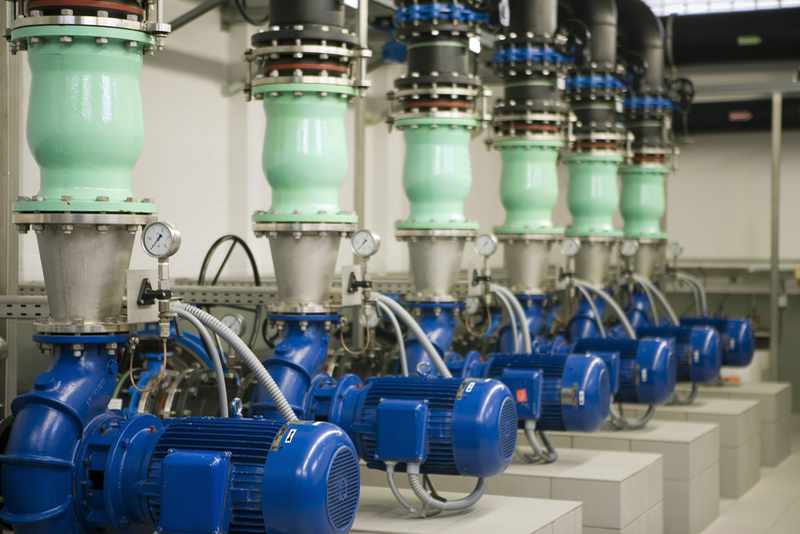
There is often an urgency to start sizing pumps based on duty point (discharge pressure required and flow). However, identifying the above basic fluid parameters will help define the application, ensuring the correct pump is specified the first time.
For instance, if the fluid is corrosive, a pump with corrosion-resistant materials such as stainless steel or plastic components may be necessary. For abrasive fluids, pumps with hard-wearing materials or those equipped with abrasion-resistant coatings are preferable. Additionally, temperature-sensitive fluids may require pumps with specialized seals or cooling mechanisms to prevent damage or overheating.
2. What is the Flow Rate Requirement?
With fluid properties of the fluid defined, flow rate and discharge pressure are essential for sizing the pump correctly.
Calculate the flow rate based on the specific application requirements. This can be done by considering factors such as the volume of fluid needed per unit of time and any variations in flow rate during operation. Ensure the selected pump’s performance curve aligns with the required flow rate at the operating conditions of your system.
3. What is the Total Head Requirement?
Total head refers to the total energy required by the pump to overcome resistance in the system, including friction losses, elevation changes, and pressure requirements. Understanding the total head requirement is crucial for selecting a pump that can provide sufficient pressure to meet the system’s demands.
It is not the purpose of this post to instruct the reader how to calculate total head of the application. That will be covered on a future blog post and in the meantime there are several online articles and examples on how to calculate this value. We will restrict this to a qualitative understanding of the factors that are considered when calculating the total head required by the application.
- Static head (elevation change)
- Dynamic head (friction losses)
- Pressure head (system pressure requirements)
Ensure the selected pump’s performance curve intersects with the total head requirement at the desired flow rate to ensure optimal performance and efficiency.
4. What is the Power Source Available?
Consider the availability and compatibility of power sources when selecting an industrial pump. Determine whether electric, diesel, gasoline, or pneumatic power is readily accessible and feasible for your application.
Electric driven pumps – Commonly used for stationary applications with access to electrical grids. Electrical requirements, like fluid properties must be understood:
- Phase
- Voltage
- Frequency
- Full Load Amps
Diesel or gasoline-powered pumps – Preferred for remote or mobile operations where electricity may not be available
Pneumatic pumps – Often used in industrial facilities where plant air is available or electrical power is inconvenient (remote mine locations).
5. What is the Required Pump Efficiency?
Efficiency is an often overlooked but critical factor in pump selection as it directly impacts operating costs and energy consumption. Higher efficiency pumps can result in significant long-term savings by reducing energy consumption and maintenance costs.
The most basic way to evaluate a pumps efficiency is to look for the efficiency curves included on the manufacturers pump curve. However, this efficiency is relative. It ignores differences in electrical options (high efficiency motors, VFDs, etc.) and pump technologies (multiple stages, PD vs centrifugals, etc.).
6. What are the Installation and Maintenance Requirements?
Consider the ease of installation, operation, and maintenance when selecting an industrial pump. Complex installation procedures or frequent preventative maintenance requirements can increase downtime and operational costs.
Choose a pump that is easy to install, operate, and maintain. Look for features such as accessible components, simple maintenance procedures, and availability of spare parts. Additionally, consider factors such as pump accessibility, space requirements, and any specialized tools or expertise needed for installation and maintenance.
7. What is the Pump’s Reliability and Durability?
Reliability and durability are crucial considerations, especially in industrial environments where downtime can be costly. Selecting a pump with a proven track record of reliability and robust construction can minimize the risk of unexpected failures and costly repairs.
Research the pump manufacturer’s reputation, product reviews, and warranty terms to assess reliability and durability. Of course most manufacturers will shout from the rooftops declaring their products superiority, so don’t be afraid to ask your product representative for referrals.
8. What are the Safety Considerations?
Answering the first 3 questions in this guide will ensure most safety considerations are accounted for, however considering safety features such as leak detection, overpressure protection, and compliance with relevant safety standards and regulations is always recommended.
Choose a pump with built-in safety features designed to mitigate risks associated with fluid handling, such as leakage, over-pressurization, or equipment failure. Ensure the pump complies with industry standards and regulations applicable to your specific application, such as ANSI, API, or ATEX standards for hazardous environments.
9. What is the Total Cost of Ownership (TCO)?
In addition to the initial purchase price, consider the total cost of ownership over the pump’s lifespan, including energy consumption, maintenance, repair, and replacement costs. Opting for a pump with lower TCO can result in significant cost savings over time.
Calculate the TCO by considering factors such as purchase price, energy efficiency, maintenance requirements, expected lifespan, and potential downtime costs. Compare TCO estimates for different pump options to identify the most cost-effective solution for your application. Investing in a higher-quality pump with lower operating costs and longer lifespan may yield greater savings in the long run.
10. What Technical Support and Services are Available?
Consider the availability of technical support, training, and aftermarket services when selecting an industrial pump. Reliable technical support and prompt service can ensure smooth operation, troubleshooting, and timely maintenance.
Choose a supplier that offers comprehensive technical support, training programs, and aftermarket services. Look for features such as 24/7 customer support, on-site assistance, and access to spare parts. Establishing a relationship with a reliable service provider can help minimize downtime and ensure the continued performance of your pump system.
Selecting the right industrial pump requires careful consideration of various factors, including fluid properties, flow rate requirements, total head, power source, efficiency, installation and maintenance requirements, reliability, safety, total cost of ownership, and available technical support. By answering the 10 questions above with the help of your technical sales engineer, you can make an informed decision and choose the most suitable pump for your application.
You can also reach out to us with any questions you have or ask for a quote.