10 Common Mistakes to Avoid with Industrial Pumps: A Comprehensive Guide
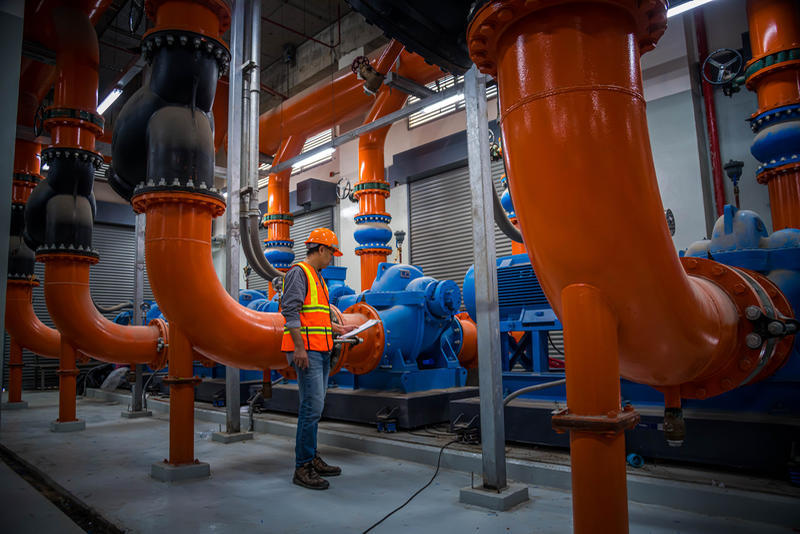
Industrial pumps are the unsung heroes of numerous manufacturing processes, ensuring the smooth flow of fluids in various industries like oil and gas, chemical processing, water treatment, and more.
Despite their crucial role, pumps often encounter issues due to common mistakes made during their operation and maintenance. In this comprehensive guide, we’ll delve into the ten most common mistakes people make with industrial pumps and provide actionable insights on how to avoid them.
1. Neglecting Regular Maintenance:
One of the primary mistakes people make with industrial pumps is neglecting regular maintenance. Like any machinery, pumps require periodic inspection, lubrication, and cleaning to ensure optimal performance and longevity. Ignoring maintenance schedules can lead to premature wear and tear, decreased efficiency, and costly downtime.
2. Incorrect Installation:
Improper installation is another common mistake that can significantly impact pump performance. Factors such as incorrect alignment, inadequate foundation, and improper piping can lead to vibration, cavitation, and other operational issues. It’s essential to follow manufacturer guidelines and enlist the expertise of qualified professionals during the installation process.
3. Overlooking Pump Selection:
Choosing the wrong pump for a specific application is a critical mistake that can result in inefficiency and increased operating costs. Factors such as flow rate, head pressure, fluid viscosity, and temperature must be carefully considered when selecting a pump. Consulting with pump specialists and conducting thorough research can help avoid this costly error.
4. Ignoring Operating Conditions:
Failure to consider operating conditions such as temperature, pressure, and environmental factors can lead to pump failure and safety hazards. Pumps should be operated within their specified operating range to prevent overheating, corrosion, and other adverse effects. Monitoring operating conditions and implementing appropriate safeguards are essential for maintaining pump reliability.
5. Poor Fluid Management:
Improper fluid management, including inadequate filtration, contamination, and improper fluid handling practices, can degrade pump performance and lead to premature failure. Regular fluid analysis, proper filtration systems, and adherence to recommended fluid handling procedures are essential for maximizing pump efficiency and longevity.
6. Lack of Training and Knowledge:
Insufficient training and knowledge among personnel responsible for pump operation and maintenance can contribute to avoidable mistakes and safety hazards. Investing in comprehensive training programs and ensuring staff members are adequately equipped with the necessary skills and knowledge can mitigate the risk of errors and downtime.
7. Delayed Repairs and Maintenance:
Ignoring signs of pump malfunction or delaying necessary repairs and maintenance can exacerbate issues and lead to costly breakdowns. It’s essential to address any abnormalities, unusual noises, or performance deviations promptly and conduct preventive maintenance according to schedule to prevent minor issues from escalating into major problems.
8. Improper Pump Priming and Venting:
Inadequate priming and venting procedures can result in air pockets within the pump, causing cavitation, reduced efficiency, and potential damage to pump components. Proper priming and venting techniques should be followed to ensure the pump is fully filled with fluid and free of air before operation, thereby optimizing performance and preventing damage.
9. Neglecting Pump Monitoring and Condition Assessment:
Failing to monitor pump performance and conduct regular condition assessments can leave operators unaware of potential issues until it’s too late. Implementing predictive maintenance techniques such as vibration analysis, thermography, and oil analysis can help detect early signs of deterioration and schedule maintenance proactively, minimizing downtime and repair costs.
10. Lack of Spare Parts and Redundancy:
Finally, not having an adequate inventory of spare parts and redundancy measures in place can prolong downtime in the event of pump failure. Maintaining a stock of critical spare parts and having backup pumps or systems on standby can expedite repairs and ensure continuity of operations during emergencies.
Industrial pumps play a vital role in numerous industrial processes, and avoiding common mistakes is essential for maximizing their efficiency, reliability, and lifespan. By prioritizing regular maintenance, proper installation, careful pump selection, and adherence to operating guidelines, operators can mitigate risks and optimize pump performance. Investing in training, monitoring technologies, and spare parts inventory can further enhance pump reliability and minimize downtime, ultimately contributing to improved productivity and cost savings for industrial operations.
You can also reach out to us with any questions you have or ask for a quote.