High Temperature Submersible Shredder Pumps – BJM’s Answer for Wastewater Management at Sheraton Hotel In Denver, Colorado
The Challenge
Food service environments are inevitably hard on equipment and potato chip production is no exception. The two production lines at Condor involve a maze of conveyors and chutes to move the potatoes along during the various stages of processing, which also involves a lot of water. On a normal day Condor processes approximately 120,000 pounds of potatoes, including sweet potatoes.
The raw tubers are delivered by the truckload to the factory where they are initially washed to remove dirt, rocks and other debris. The potatoes are then peeled and sliced and washed again to release and remove the potatoes’ starch. All along the production process, water is used to wash, move and rinse the potatoes.
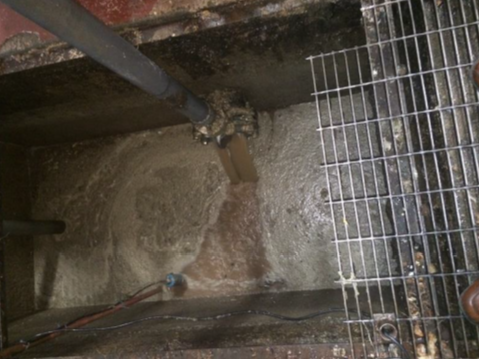
Spent water flows off the equipment, and along with the debris from the initial wash, the starch and the potato peels flow into drains in the floor that then flow with their cargo into a sump. In addition, the potato chip fryers are washed down once a week with 180-degree water and caustic beads to clean the equipment and remove the various oils used in frying. Condor uses six different types of oils in its chip making, and each has different properties, explained Kevin Kobza, long-time maintenance manager at the Condor plant. This hot caustic liquid and the oils it cleans also flow into the sump and are added to the mix that then needs to be pumped out.
The quality of the debris in the sump has been problematic for Condor. Not only do the potato peels and other debris tend to clog pumps, but the weekly caustic hot-water cleaning creates an added difficulty for most pumps. Condor previously was using a non-clog pump to pull product from the sump, but had been dealing with daily clogging issues that required the front cover of the pump to be removed and cleaned multiple times a day during production.
Maintaining a “Green” Commitment
Consistent with parent company Utz’s earth friendly philosophy, process waste and things such as paper and packaging are recycled or repurposed as much as possible. For example, potato peels and spent oils go to a local cattle feed lot. Solenoid valves have been installed on the potato peelers and other wash systems so that they turn off when they’re not needed, saving precious water. Cardboard boxes are broken down, baled and recycled. And Kobza is in the process of changing out lighting in the factory to be more energy efficient.
“We’re trying to conserve, and I try to do whatever I can to save a little here and there,” Kobza said. In light of these efforts to operate efficiently, it was especially frustrating to have to clear the pump two to four times during a 16-hour shift.
The Solution
Condor has a long-standing relationship with Denver Industrial Pumps, a local distributor of BJM Pumps. Phoenix Sullivan is the representative on the Condor account. To address the specific challenges of the Condor sump, Sullivan recommended one of BJM’s newer SKGF Series submersible shredder pumps that use its new patent-pending RAD-AX® dual shredding technology. An SKG37CF 5-HP high temperature/high endurance high performance shredder pump was installed in the Condor plant in the first quarter of 2016. The BJM cast iron F-Series submersible pumps are specifically designed to be installed in sumps where liquids are too hot for other submersible pumps.
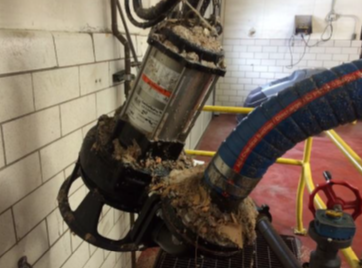
The SKGF solved Condor’s issues with clogging and build up around the pump. The original pumps were self-priming, an older style technology with a more challenging configuration for this type of application. Condor’s self-priming pumps sat outside the sump. A pipe from the sump sucked liquids up to the pump, but it was highly prone to clogging from the potato solids, explained Ben Wells, BJM Regional Manager.
“The BJM submersible pump puts the pump and shredder down at the bottom of the sump. It reduces the solid size before it enters the piping system. This has all but eliminated the clogging,” Wells said. “The self-primer was used because other submersibles could not handle the hot water from the fryer cleaning. The BJM high temperature submersible pump solved both the high temperature and clogging issues.”
The high-temperature motor, suitable to handle 200oF liquids, also allows the pump to handle the hot caustic washdown cycle without damaging the motor. After one year, the pump has been shut down for one planned maintenance event, but there have been no clogs or other downtime.
Sullivan said BJM had beefed up the series design by trimming the impeller, which allowed a larger motor and higher torque in a compact housing that still had room for the dual radial and axial shredding elements. Condor was one of the first installations of the SKGF with RAD-AX® technology.
The SKGF is designed to obliterate flushable wipes and other difficult solids in high temperature situations. Items previously considered difficult or near impossible to pump are effectively handled through the innovative design. The robust construction prevents downtime and reduces maintenance for longer life.
Additional Features of the SKG F Series:
- High temperature/high endurance construction for challenging environments.
- All shredding elements constructed of hardened 440C Stainless Steel with a Rockwell hardness of 55C plus.
- Shredding System efficiency to alleviate potentially high surge load to the motor.
- Efficient, high solids passage impeller and volute design, coupled to a high torque 4-pole motor that comes in 2, 3 and 5 horse power.
- Oil-lubricated double mechanical seals and separate lip seal to protect the motor.
- High temperature rated Santoprene power cable and Seal Minder cable – seal oil leak detector.
- Choice of two impeller trims for each SKGF model to expand hydraulic coverage. The hardened impeller and plate materials provide maximum wear resistance for long service life and hardened cast iron construction stands up to rough handling, pumping gritty water and the effect of abrasives.
Winding protection and NEMA Class R motor insulation allow motor temperatures to rise to 428°F, superior to pumps with Class A and B insulation, allows the pump to handle liquids to 200°F. Thermal switches embedded in the motor will cut power to the pump should the temperature of the windings rise too high. When the motor cools the switch will automatically reset and the pump will turn back on.
The Outcome
The customer is thrilled with the performance and reliability.
Written by: Mike Bjorkman in conjunction with Phoenix Sullivan, Outside Sales, Denver Industrial Pump; and Ben Wells, Regional Manager, BJM Pumps