Predictive Maintenance for Industrial Pumps: The Future of Reliable Operations
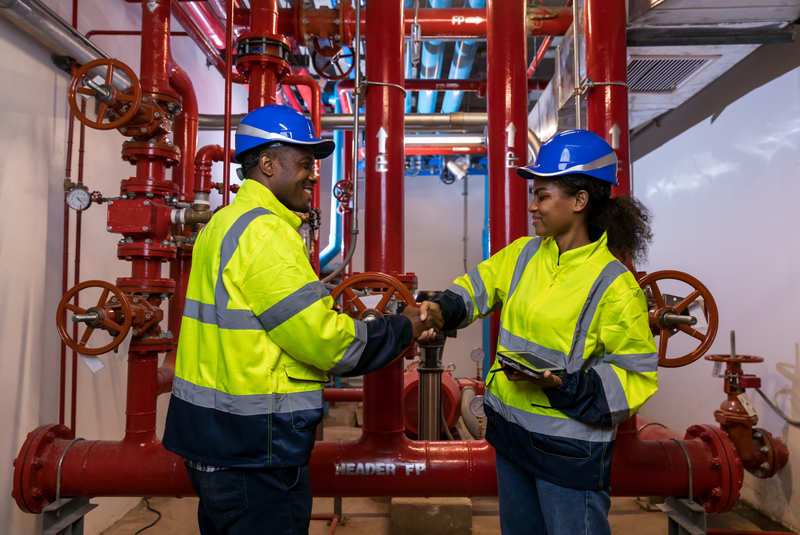
Adopting predictive maintenance (PdM) for industrial pumps is revolutionizing facility reliability. By shifting from reactive or scheduled maintenance to sensor-based, data-driven strategies, manufacturers and plant managers can cut downtime, optimize performance, and reduce costs. In this post, we explore why predictive maintenance industrial pumps is gaining traction and how you can implement it.
Why Predictive Maintenance Industrial Pumps Matters
From Reactive to Proactive Maintenance
Traditional reactive maintenance—fixing pumps only after failure—and preventive maintenance—based on time intervals—are both suboptimal. Reactive approaches lead to costly downtime, while preventive methods often involve replacing parts prematurely.
Predictive maintenance forecasts issues before they occur using sensors, analytics, and machine learning. A study using an edge-based convolutional neural network showed significant early failure detection from vibration data analysis .
Key Benefits of Predictive Maintenance
- Reduced downtime & OPEX – Predicting failures minimizes unscheduled outages and repairs .
- Extended pump life – Timely interventions avoid collateral damage and extend mean time between failures (MTBF) .
- Energy efficiency – Detecting misalignment, cavitation, or worn impellers early prevents inefficiencies (powersyourteam.com).
How Predictive Maintenance Industrial Pumps Works
Sensor Data Collection
Equip pumps with sensors to monitor vibration, temperature, pressure, flow, and motor current. These sensors feed critical real-time data about system health.
Edge Analytics & Smart Sensors
Edge devices like low-complexity CNNs process data on-site, minimizing response time and bandwidth (arXiv). IoT-enabled pumps with built-in monitoring capabilities are becoming common (arXiv).
Cloud Analytics & AI Integration
Cloud platforms aggregate data across facilities, applying AI and ML for anomaly detection and remaining useful life (RUL) estimation. Predictive insights trigger alerts for operators to act before failure.
Implementing a Predictive Maintenance Strategy
Step-by-Step Guide
1. Baseline Assessment
Begin by analyzing historical performance data—vibration trends, repair logs, and downtime events. This helps identify critical failure modes to monitor.
2. Sensor Selection and Installation
Select sensors based on your pumps’ needs. Vibration sensors for rotating equipment, thermal sensors for bearings and seals, and pressure sensors for cavitation detection.
3. Edge Processing Deployment
Install local controllers that can detect anomalies and send summarized alerts to the cloud.
4. Cloud Platform & Dashboard
Use a cloud analytics solution with visualization dashboards, configurable alerts, and integration capabilities with your CMMS or SCADA system.
5. Staff Training & Workflow Integration
Train personnel to respond to alerts and update maintenance workflows to include sensor-driven checks.
6. Continuous Improvement
Refine analytics models using ongoing data, update thresholds, and expand the program to other pumps or systems.
Case Study: A Pumping Station Success
A wastewater facility implemented predictive maintenance using vibration sensors and machine learning. They achieved:
- 16.7% reduction in energy use
- 97% fewer alarms
- Early detection of impeller wear and seal leaks
(powersyourteam.com, arXiv)
This demonstrates both cost savings and environmental benefits.
Avoiding Common Pitfalls
- Don’t install willy-nilly – Sensor placement matters; focus on bearings, shafts, and seals.
- Edge and cloud work together – On-site processing for fast detection; cloud for trends and ML.
- Having alerts without workflow is useless – Ensure alerts trigger action (e.g., lubrication checks, alignment correction).
- Start small, scale smart – Pilot one critical pump, evaluate ROI, and scale gradually.
Resources to Explore
- Guide to IoT-based industrial pump monitoring (CRI Groups – WHAT ARE YOU LOOKING FOR?)
- Predictive maintenance system architectures
Related Reading
- Learn more about traditional industrial pump maintenance best practices in our internal post: How Preventative Maintenance Extends the Life of Your Industrial Pump
Implementing predictive maintenance industrial pumps is no longer a futuristic concept—it’s a proven approach to reduce downtime, optimize performance, and save money. Armed with sensors, analytics, and AI, you can outsmart failures before they happen and strengthen operational resilience in 2025 and beyond.
About the author: Denver Pumps SEO Team – focused on delivering cutting-edge content on industrial pump solutions.