BJM Shredder Pumps To The Rescue
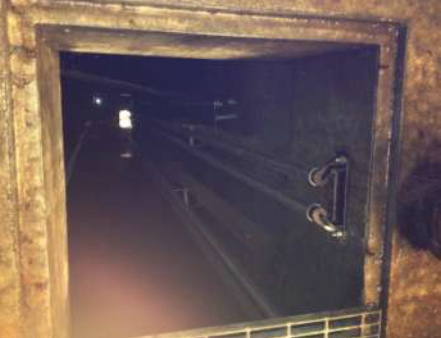
The Challenge
During baseball season, the water and any trash and debris collected with it is pumped up and out of the vault and into the storm sewer system. In the off season, a much smaller amount of collected water is pumped out and diverted to any of several small detention ponds to evaporate.
The pumps that do the heavy lifting of moving all the collected water out of the vault were replaced in May 2015. The original pumps were chopper pumps installed in 1998. Although they were showing signs of wear — moisture was getting in the motors — they weren’t replaced.
When it became evident that the old pumps needed to be replaced, Young and James Leflar, an engineer and member of the HVAC team at Coors Field, reached out to Phoenix Sullivan, their contact at Denver Industrial Pumps.
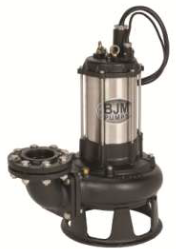
The Solution
Sullivan recommended the old chopper pumps be replaced with two BJM SK55C Shredder Pumps and the associated electric submersible sump pump package. An integral part of the new solution was a variable frequency drive (VFD) control panel that was customized by BJM to be compatible with Coors Field’s existing alarm panels in the security room.
“The customer needed a pump that could handle debris getting into the vault/sump and not clogging the pump,” Sullivan said. “The BJM shedder pump has a cutting tool that cuts and shreds the debris . . . allowing it to pass without clogging the pump.” In addition to their ability to handle debris, other technological improvements also made the BJM shredder pumps a good solution. For one thing, the original pumps operated on a highly specialized and outdated air bubbler system, whereas the SK55C pumps use a simple float system to turn them on and off.
The BJM pumps operate on a lead–lag setup, Sullivan explained. The floats prompt the first pump to turn on, and if needed, also prompt the second pump to turn on. Likewise, the floats shut the pumps off when the water level is sufficiently lowered. For this installation, the target flow for each pump is approximately 350 gpm at 32 feet of total dynamic head. Generally, the BJM SK55C can handle a maximum flow of 570 gpm, with a maximum head of 59 feet.
The two pumps sit in a sump that’s approximately 16 feet deep. In addition to the two 7.5 HP pumps, this BJM sump package included two cast-iron slide rail assemblies, four stainless steel intermediate guide rail brackets, and 100 feet of 1.5 inch stainless steel pipe rails.
The newer pumps’ also take full advantage of advances in metallurgy and materials that allow all of the pump’s parts and components to be self-contained, Sullivan said. The only parts that may experience wear are the cutting bars, bearings, and seals. Those components aside, it would be realistic to expect these pumps to last 20 years.
BJM’s shredder pumps leave solids slightly larger than if passed through a grinder pump. The shredding action is caused by using a cutting impeller with a Tungsten Carbide Tip, against a “spiral” shaped diffuser plate.
Additional technical features of the BJMs Shredder pumps include:
- Longer Power Cord — A 33-foot power cord is standard
- 304SS Motor Housing — The stainless steel motor housing provides superior abrasion resistance and will not wear out like aluminum motor housings when pumping sandy water.
- Three Seal Motor Protection — The motor is protected by double mechanical seals. The lower seal is made of silicon carbide/silicon carbide, and the upper seal is made of carbon/ceramic. An additional lip seal has been installed above the impeller to help prevent abrasives such as dirt, silt or sand from entering into the seal chamber.
- More Motor Protection — Winding protection and (NEMA) Class F motor insulation allows the motor temperature to rise to 230°F, superior to pumps with Class A and B insulation. An automatic switch turns the pump motor off if the temperature and/or amp draw gets too high. When the motor cools the switch will automatically reset and the pump will turn back on.
- Tough Pump Construction — Hardened cast iron stands up to rough handling and pumping sandy water unlike pumps with soft resin impellers or plastic exterior components.
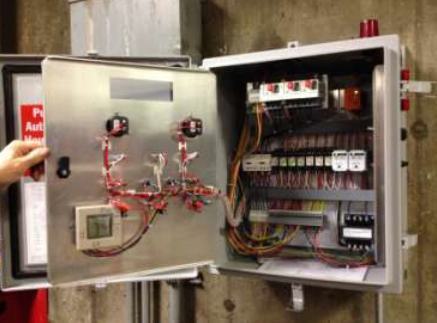
The pumps are also available in 316 cast stainless steel, and a new explosion proof shredder pump is also now available.
Another Advantage
BJM was also willing to go the extra mile to create a custom control panel so the ballpark could tie into its existing alarms in the security room. The Custom Duplex Control Panel BJM fabricated has auxiliary contacts allowing communication with the existing system that includes seal minders, elapsed time meters, and dedicated auxiliary contacts for seal fail 1, seal fail 2, overload 1, overload 2, and high level.
The Outcome
As a new baseball season draws near, the HVAC team at Coors Field feels confident that with the newly installed pumps they’ll be ready to handle any curveballs that may come at them. “It does exactly what it’s supposed to do. It was a good install and we haven’t had any issues with them,” said Leflar. “They’ve done what we asked them to do and they met our criteria.”
Written by: Mike Bjorkman in conjunction with Phoenix Sullivan, Outside Sales, Denver Industrial Pump; and Ben Wells, Regional Manager, BJM Pumps